G1 at 10: the prominent reed and chanter maker celebrates a decade (video)
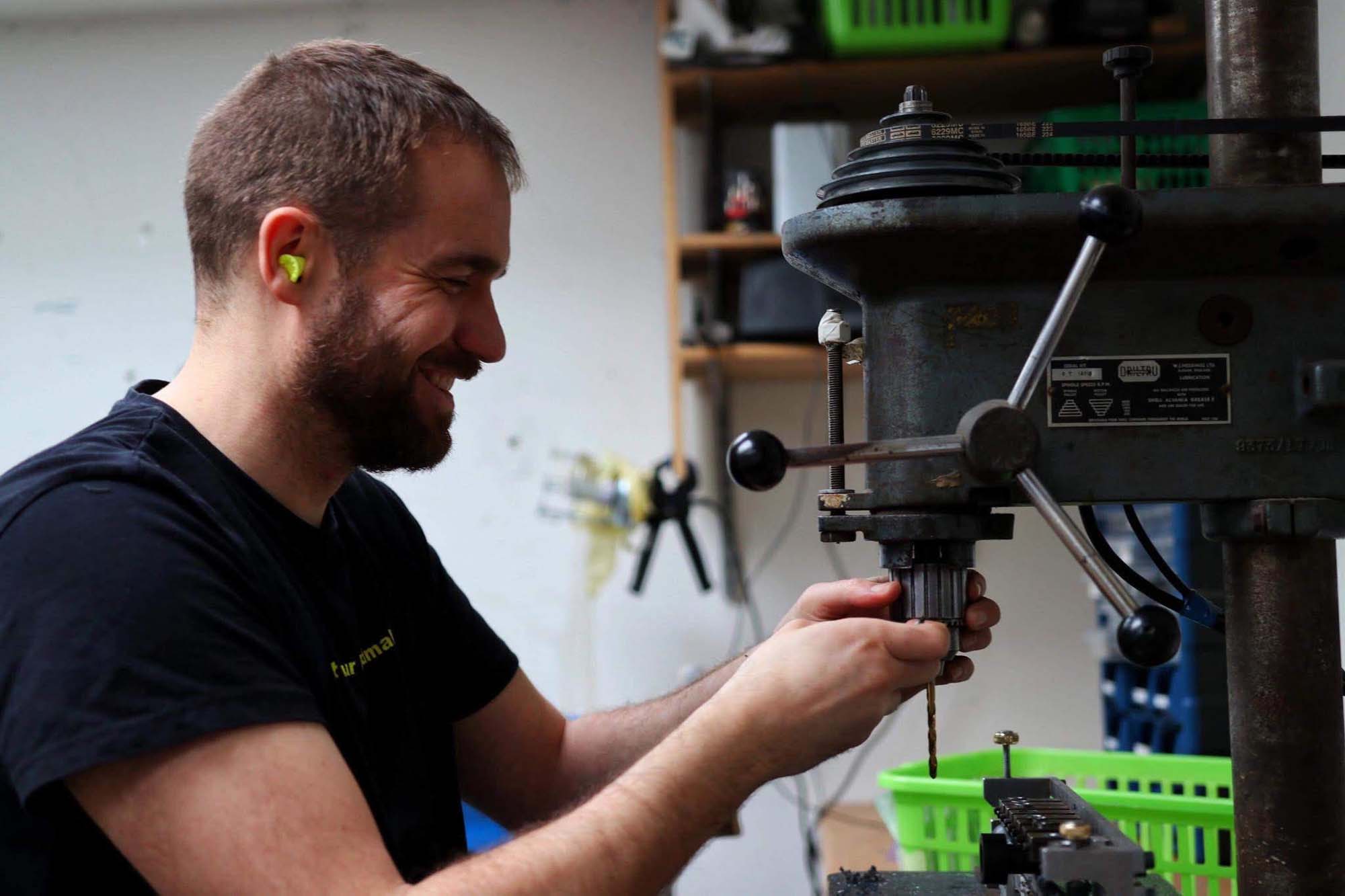
It didn’t dawn on us until we talked with owner John Elliott that G1 Reeds & Chanters of Kirkcaldy, Scotland, was named for “Grade 1” – right out of the gate in 2010 setting the company’s sights on the very top.
This year celebrating its tenth anniversary since Elliott took the plunge into full-time reedmaking, G1 is a model success story in a highly competitive and still expanding market. Indeed, after only seven years in business, the company saw Inveraray & District win the 2017 World Championship playing the company’s chanters.
Younger pipers might think of G1 as a more established maker, famed for outfitting bands like twice World Champions Inveraray & District. But before then, the market was even harder to crack.
Going back a few decades, bands and solo pipers had relatively few options for quality chanter reeds and chanters. Only a handful of makers dominated the market.
The environment changed slowly, where today, it’s nearly impossible to know who’s playing what, and the instances of manufactures judging are far fewer.
John Elliott learned his piping and his reedmaking from the legendary Bob Shepherd of Fife, who died last year at the age of 81.
Bob Shepherd, 1938-2019
October 25, 2019
“My bagpiping journey started when I had the opportunity to learn the bagpipes at Benarty Primary School in Ballingry, where I grew up,” Elliott says. “My mother had always wanted myself and my younger brother to learn a musical instrument, so when Bob Shepherd turned up, asking who wanted to learn the bagpipes, I jumped at the chance.”
In the big picture, Elliott was one of the hundreds of youngsters who Shepherd recruited and then taught to play the pipes, creating over 50 years one of the most effective teaching systems in history. The program was so popular that Shepherd had to be relatively selective. He couldn’t teach them all.
“Bob had only agreed to teach eight pupils from the class,” Elliott adds. “He came into the school once a week to teach the lucky kids who were initially selected. I was persistent and approached Bob every week, asking if I could learn to which he replied, ‘You’ll need to wait until someone gives up, son, I’ve only got eight chanters.’ This carried on for several weeks until eventually, I got my chance, which I grabbed with both hands.”
A man who led a group of teenaged students to the height of the pipe band universe when Grade 1 Dysart & Dundonald won World Championships in 1978 and ’79, Shepherd could spot talent and commitment when he saw it.
“Back then, I didn’t put the practice chanter down!” Elliott says. “Along with me in that bunch of learners was Bob’s nephew, George Shepherd Jr., who then went on to lead Grade 1 Clan Gregor Society and City of Whitehorse. I also learned alongside David Colvin, the writer and star of the recently famed ‘Thunderstruck’ play.
“We were all great friends but also very competitive, whether it be learning the scale before everyone else, learning our first tunes ‘The Brown Haired Maiden’ and ‘Mari’s Wedding’ while trying to play all the embellishments. I recall getting my first set of pipes, which were plastic, along with another five pipers at Denend Primary School in Cardenden where the adult Dysart & Dundonald band practised on a Friday. Bob challenged us all by saying, ‘Well, who can get a noise out them first.’ I remember it being me, but David Colvin said it was him, which led to a bit of an argument followed by more blowing and squeaking. We all played together for many years with Lochgelly High School while also being taught and led by Pipe-Major Tom Brown. The band were a great bunch and won several World Championships and Champions of Champions titles at Novice Juvenile and Juvenile grades.”
While Bob Shepherd was a part-time teacher in the Fife area, he had established his bagpipe and reed making business, R.T. Shepherd & Son, which continues today. Shepherd chanter reeds and chanters had gained significant traction and popularity, bands like the upstart Field Marshal Montgomery and established Shotts & Dykehead Caledonia taking to them.
The business was expanding, and Shepherd was always on the lookout for quality help. He would seek out pipers who had personal knowledge of and experience with the very products they would learn to make. Elliott was no exception.
“By the time I left school, Bob had asked me to come down and do a week helping out at Shepherd Bagpipes. I was offered a job at the end of that week! This is where I learned how to make pipe reeds, synthetic drone reeds and pipe chanters. I loved it because I could make my own reeds and also tweak things a little to try and get the best sound possible out of my own pipes. As time went on, I became more and more involved in product development and testing, as I was always keen to experiment and improve.
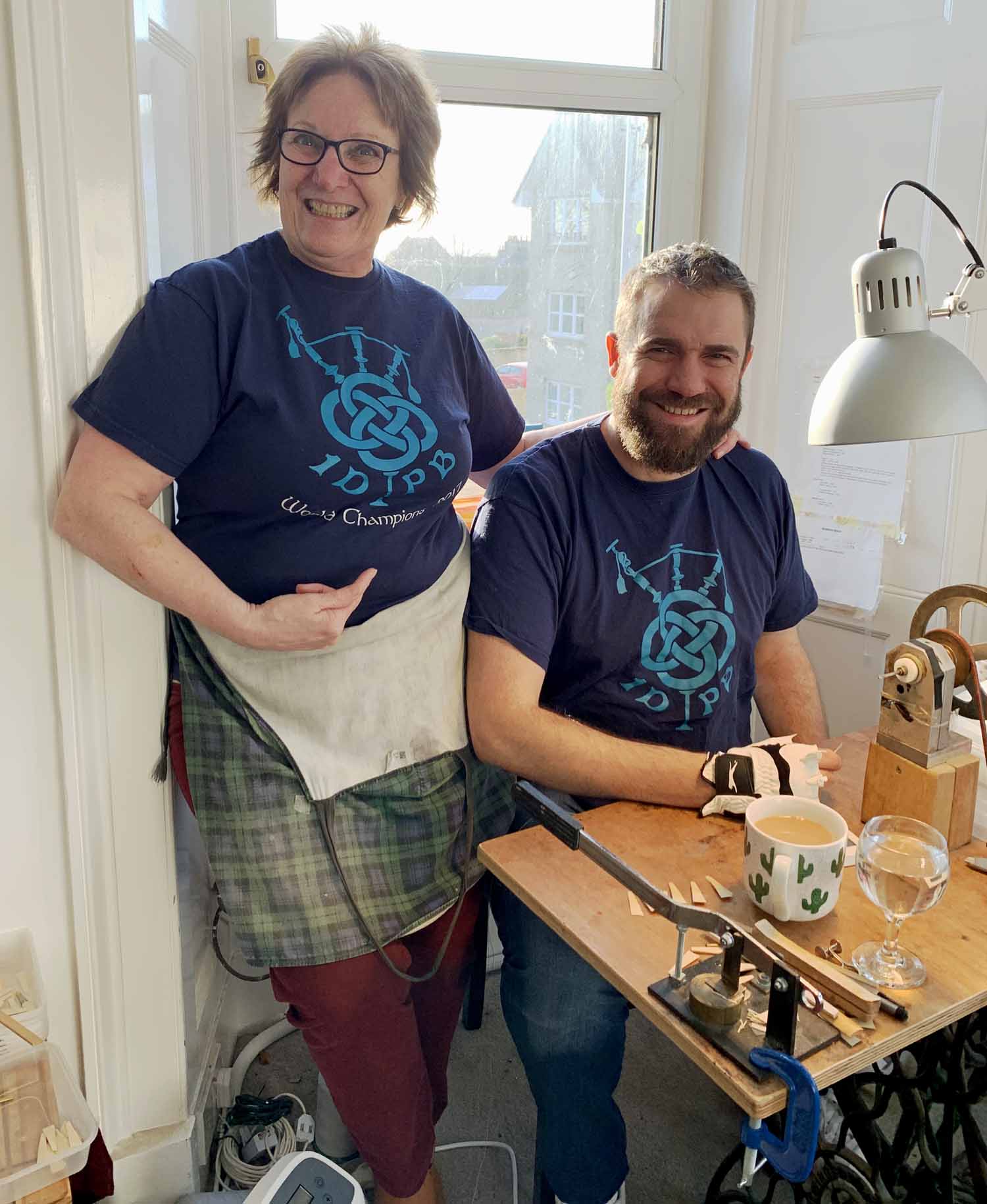
“After 17 years in Shepherd’s, I decided to go my own way and start G1 Reeds. I started out making cane drone reeds, which was something a good friend of mine, Bob Hain, had shown me. As they became popular, more and more people were asking me to make pipe reeds as they were struggling to get a supply of good reeds. I then began gathering the necessary machinery and set about designing the G1 original pipe reed. The reeds began to get a pretty good reputation, and I was struggling to keep up with orders, so I took on my first employee: my mum! She would prepare the cane, helped with varnishing and hemping, and she still works at G1 to this day. The G1 Platinum reed followed a couple of years later.”
The company quickly expanded, as the reputation of the reeds grew. More bands and solo pipers wanted to try the products, and soon G1 Reeds launched a new pipe chanter.
“The business continued to grow as demand kept increasing. I then took on my second employee, Jamie Elder, who is now Senior Reed Maker. Throughout the years, we have continued to take on more staff when required, and we now have ten members of staff, most of whom live locally. Two of the early employees, Mikey Brown and William Wallace, came from the local Kirkcaldy & District Pipe Band, which was at the time led by Pipe-Major George Wallace. He was also one of G1 Reeds’ first-ever customers of our Platinum Chanters. Both Mikey and William are still full time and very valuable G1 employees.”
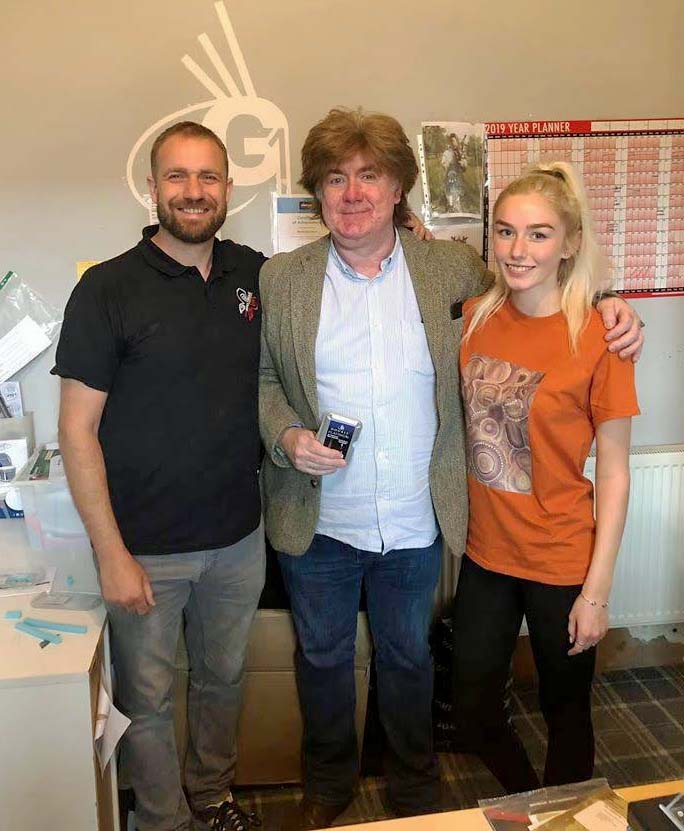
When only 15 or so years ago, pipers and pipe bands were resigned to the idea that a chanter reed had to be monstrously challenging to blow at first to be good eventually. An investment of weeks and even months of a physically painful blowing-in period was mandatory. In the last decade or so, that notion has all but died. Chanter reeds today are playable right out of the box, with only a little manipulation, if any, needed.
“There are a lot of ways to manipulate a pipe reed, but I wouldn’t recommend any of them unless you’re willing to take the chance of ruining the reed. Ideally, pick a reed that you don’t need to manipulate. Once you’ve tried one or two reeds from any supplier, you’ll get used to that type of reed as well as the strength that suits you.”
In what is a competitive business that revolves mainly around competition, Elliott is remarkably willing to offer advice, show tricks of the trade and respectful of other manufacturers. He collaborates with other makers from time to time, and as a piper with Inveraray & District enjoys the camaraderie of the UK pipe band scene.
After a decade of managing the rapid rise of G1 Reeds & Chanters, John Elliott is excited about the future.
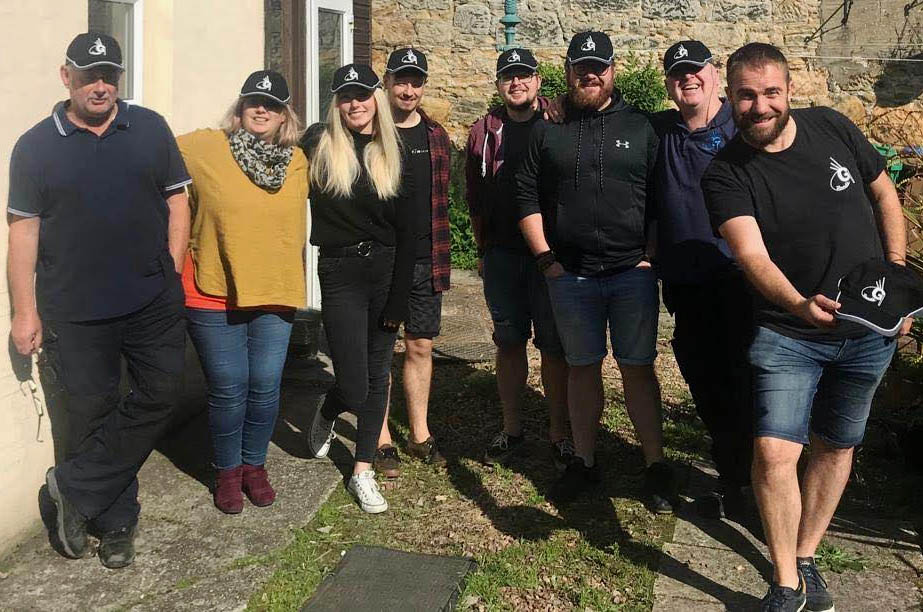
“Hopefully, the next ten years for G1 Reeds will be as special as the first. We intend to keep producing our current product range to as high a level as possible and move with the times to add new products as and when required. We have recently released a range of new chanters to the Highland bagpipe and Breton markets and will be working on some other projects.”
Not surprisingly, Elliott wants to be sure that others are recognized for their part in the company’s success.
“I would like to take this opportunity to thank everyone who has helped G1 Reeds along the way and I’m excited to see what the future holds for the business.”
Okay, time to subscribe or donate to pipes|drums so we can access everything in our 6,000-plus stories archive and keep articles and videos like this coming to you. Thanks!
Related
G1 Reeds comes up with solution for sanitary reeds
March 26, 2020
G1 helps to put Grade 1 piper back on the pipes
September 18, 2018
G1 acquires Trap Dri, becomes sole distributor of V3 moisture control products
August 10, 2018
Business unusual: How piping and drumming manufacturers and dealers are adapting
March 29, 2020
G1 Reeds John Elliott’s Tips for Selecting a Chanter Reed
Make sure there’s a nice curvature. If you can drive a bus between the blades, then it won’t be vibrating efficiently so you won’t get a nice sound. Likewise, if the blades are too closed then it won’t sound great.”
Ideally, you want a reed that has a full rich top hand with minimal tape on each note. The less tape you have on high G would indicate a reed that’s vibrant, as long as the C and F are not flat, then you’re probably onto a good reed. Also focus on getting a nice ringing high A, not to be confused with a harsh rasp or crow. This will be more evident in the pipes.”
Select a reed that’s the correct strength for you. It’s a misconception that pipers should pick a reed that they can hardly get a sound from. You need to be comfortable when playing, so try to pick a reed that you can blow a full tone from and it feels natural to you. When mouth-blowing the reed in the chanter, you should be able to play the full scale in one breath, at least five seconds of continuous blowing.
Set the reed in the reed seat of the chanter to the required depth, removing or adding a little waxed hemp if required to ensure the reed grips properly and won’t come loose while playing. If you’re using a G1 chanter and reed you can use our recommended reed depth guide to set your reed to the optimum depth in the chanter.
A good reed will sound good straight away. There’s no need to ‘blow in’ a reed for weeks or months until it sounds good or is easy enough to get through an MSR. A new reed may flatten a little more between blows than a blown-in reed, but that’s really all you should need to keep an eye on.
NO COMMENTS YET